The Pigment Dispersion Process
- By Centre Colours
- •
- 19 Oct, 2018
- •
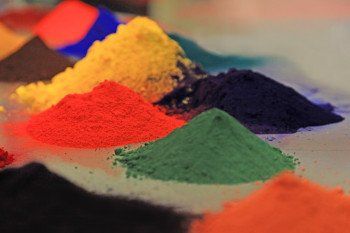
Our customers rely on us to provide them with everything needed to produce the highest quality paints, inks and coatings.
How do we do that?
By carrying out an effective pigment dispersion process.
Pigment dispersion is important to many industries that are reliant on providing quality finishes. By going through a process of wetting, dispersing and stabilising, a range of benefits can be taken advantage of:
High strength & consistent finishes
Going through a pigment dispersion process allows both the strength and consistency of pigments to be optimised. Without dispersion, flocculation can occur, which leads to patchy tones and a host of other side effects.
More cost-effective pigments
A pigment that has been run through a dispersion process ensures stability, an important factor for many commercial applications. An effective pigment dispersion process results in less pigment being needed overall, due to the quality of composition and high colour density.
Addition of innovative materials
Our saying states “Itʼs more than just colour”. This couldnʼt be truer in the addition of innovative materials within our pigments. Take graphene, for example. By adding this in during dispersion, conductivity and resistance can be integrated directly into your coating.
What is a pigment dispersion process?
This is the process of creating a stable, high-quality pigment for use in commercial applications. Let us take you through the process step by step:
Wetting
Pigments contain agglomerates. This means that particles in a pigment naturally group together, which when mixed can result in clumping and uneven shades.
The first step in the pigment dispersion process is providing the platform for these agglomerates to be broken down.
Wetting involves replacing the air and moisture between the pigment particles with a binding solution (also called a pigment dispersing agent). The binding solution gets into the spaces that are currently filled, wetting the particles in preparation for them to be dispersed.
Dispersing
Following the wetting process, the particles in the pigment are in a state ready for dispersion. Dispersion can also be referred to as de-agglomeration, as itʼs the process of breaking down the bonds between the particles.
To do this, a force greater than the surface tension of the particles is required. We achieve this by using our triple roll mill, which breaks down the agglomerates into optimal particulate sizes.
This results in single particles and very small agglomerates with a high concentration of pigment.
Stabilisation
Due to the pressure and energy involved during the pigment dispersion process, the resulting energy in the small particles over a larger surface area is incredibly high.
The particles will naturally gravitate towards each other. A stabilising agent is needed to ensure flocculation doesnʼt occur (this is similar to agglomeration, where the particles return to a state of being joined together).
This is usually introduced during dispersion, and the agent used depends on the pigment surface.
Our pigment dispersion process
The process is complex, and one that we are experts in. Over the last few years we have developed a reputation for creating pigment dispersions of the very highest quality, whether thatʼs developing new formulations or using those that already exist with our customers.
Whether youʼre looking for a large or small batch, our dispersion services are available for your bespoke needs.
Get in touch with our team for a competitive quotation today.